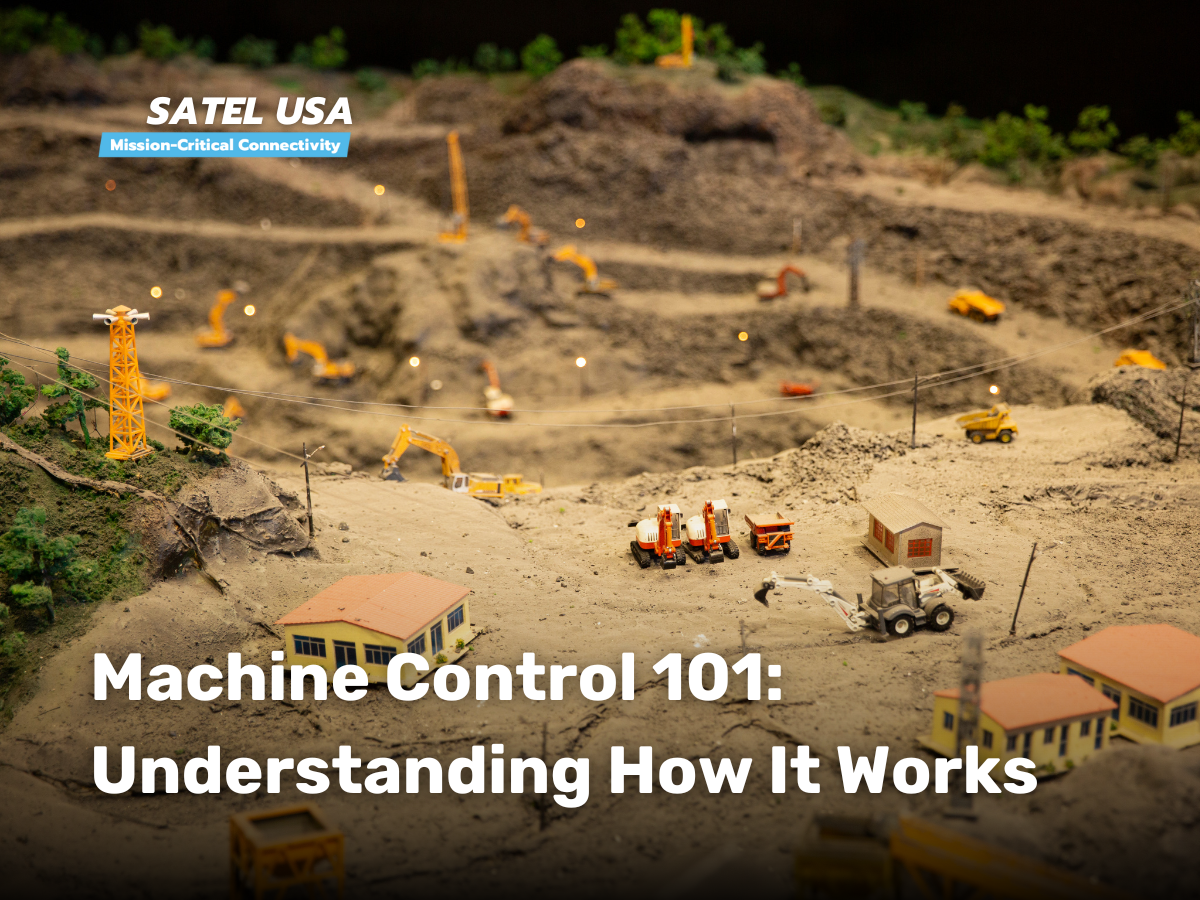
In the world of construction, agriculture, mining, and related industries, precision is everything. That’s where the power of machine control shines. Before we delve deeper into the intricate world of machine control, if you’re looking for foundational knowledge like understanding what is machine control and why it is important, our previous article, Machine Control Explained: What You Need to Know, addresses those topics and more.
Once you’re up to speed or if you’re already familiar, read on to gain a comprehensive understanding of the subject and dive deep into the mechanics and features of these systems.
Decoding Modern Construction: Machine Control Systems Explained
Positioning Fundamentals: Beginning in the Atmosphere
Precision in machine control starts high above the site in the atmosphere with GPS satellite constellations. These satellites determine their positions through triangulation, offering location accuracy down to the centimeter. Software engineers then create a digital model of the construction site. By using the precise positions of assets and machines, they sync the machinery on the actual construction site with this digital plan, ensuring the desired outcomes of the job are achieved on the ground.
Base Stations: Crucial Players on the Ground
Base stations are essential components on the construction site. They capture GPS signals and then broadcast correctional data across the job site. Whether through their built-in radios or using powerful external radios like the Satel EASy Pro+ 35W, they guarantee centimeter-level accuracy throughout the site. This level of precision is indispensable in today’s era of smart construction.
The Role of Rovers in Advanced Construction:
Rovers, equipped with advanced receivers like the internal MR-TR4+, tap into the signals and receive the correction data. The onboard computers map their location in the onboard display which shows a 3D map of the site, pinpointing their exact location on the site and guiding their actions accordingly giving the operators a competitive advantage over traditional machines
Alternative Systems:
Cellular Systems/NTRIP: These are a modern twist, leveraging cellular signals and connecting to offsite reference stations, eliminating the need for onsite base stations.
IMUs (Inertial Measurement Units): These are the unsung heroes in the background, rapidly calculating position changes and working in tandem with other systems to ensure precision in the relative location of the machine in the digital blueprint.
The Building Blocks: Components of a Machine Control System
External Components:
- Satellite Constellations: Orbiting the Earth, these are the primary sources of the GPS signals.
- GNSS Base Stations: Acting as the middlemen, they refine the signals for on-ground precision.
- Radio Base Stations: These radios, both high and low power, transmit signals across the job site from a central antenna location, often amplifying the signal for greater coverage.
- Cellular Reference Stations: A modern alternative to base stations, they provide signals over vast distances.
Rover Components:
- Rovers & Machines: While man rovers help in calibration and layout, machines like dozers and excavators reshape the landscape.
- Receivers & Antennas: They are the ears of the system, constantly listening for signals.
- Data Collectors: The brain of the operation, processes signals and guides the machinery using advanced software systems designed for precision positioning.
- Machine Blades & IMUs: While blades reshape the ground, IMUs ensure every move is measured and precise.
In Action: Machine Control Systems on the Ground
From the initial excavation to the final touches, machine control systems play a role in every step:
- Excavating: Precision digging to craft the site’s foundation.
- Paving: Guiding vehicles for perfect alignment and slope.
- Piling: Strengthening foundations by ensuring correct material placement.
- Compacting: Ensuring a firm surface, ready for construction.
- Drilling: Precision drilling, ensuring safety and accuracy.
- Dozing & Scraping: From rough leveling with dozers to fine-tuning with scrapers, machine control ensures a perfect finish.
Designing with Precision: Factors to Consider for Machine Control Systems
When venturing into the design of a machine control system, it’s not just about integrating advanced technology. It’s about ensuring that the system is robust, reliable, and tailored to the specific needs of the project. Here are some pivotal factors to consider:
- Purpose & Application:
- Understand the primary purpose of the system. Is it for excavation, drilling, paving, or another specific task? The design should cater to the primary application to ensure maximum efficiency.
- Environmental Conditions:
- Consider the typical environmental conditions of the job site. Factors like temperature extremes, moisture levels, and terrain can influence the performance of the system.
- Accuracy & Precision:
- Determine the level of accuracy required. While some projects might need centimeter-level precision, others might be more forgiving. Design the system to meet or exceed these requirements.
- Integration with Other Systems:
- Ensure that the machine control system can seamlessly integrate with other onsite systems, whether it’s data management tools, communication systems, or other machinery.
- User Interface & Training:
- The system should be user-friendly, with an intuitive interface. Consider the training required for operators and ensure that resources are available.
- Scalability & Upgradability:
- As technology evolves, so should the machine control system. Design it with scalability in mind, allowing for future upgrades and expansions.
- Safety & Redundancies:
- Safety is paramount. Incorporate multiple redundancies to ensure that in the event of a component failure, the system can still operate safely or shut down without posing risks.
- Budget & ROI:
- While it’s essential to have a state-of-the-art system, it’s equally crucial to consider the budget. Ensure that the system offers a good return on investment by improving efficiency and reducing errors.
By taking these factors into account, one can design a machine control system that not only meets the technical requirements but also ensures smooth operations, safety, and long-term value.
Bringing the Pieces into Focus
Machine control isn’t just a trend—it’s the linchpin and backbone of modern-day construction, agriculture, mining operations, and many other jobs. As you embark on the journey of precision work and aim to make your tasks smoother and more accurate, understanding the basics is essential but only the starting point. Reflect and think:
How can these insights and knowledge help elevate your daily tasks?
Are you leveraging and maximizing the potential of this groundbreaking technology to its fullest?
Consider any gaps or aspects you might be missing in your current operations and workflow that could be revolutionized by the efficiency and precision of machine control systems. The future of your job is in your hands, so ensure you’re equipped with the right tools.
To ensure you’re at the forefront of this technological evolution and to discover how machine control can elevate your projects, subscribe to our newsletter or reach out to our expert team for personalized advice and solutions. We’re an authorized dealer for Satel Radios in the USA, our mission is to provide reliable wireless communications hardware in Machine Control Systems and other mission-critical applications. We’re here to help.