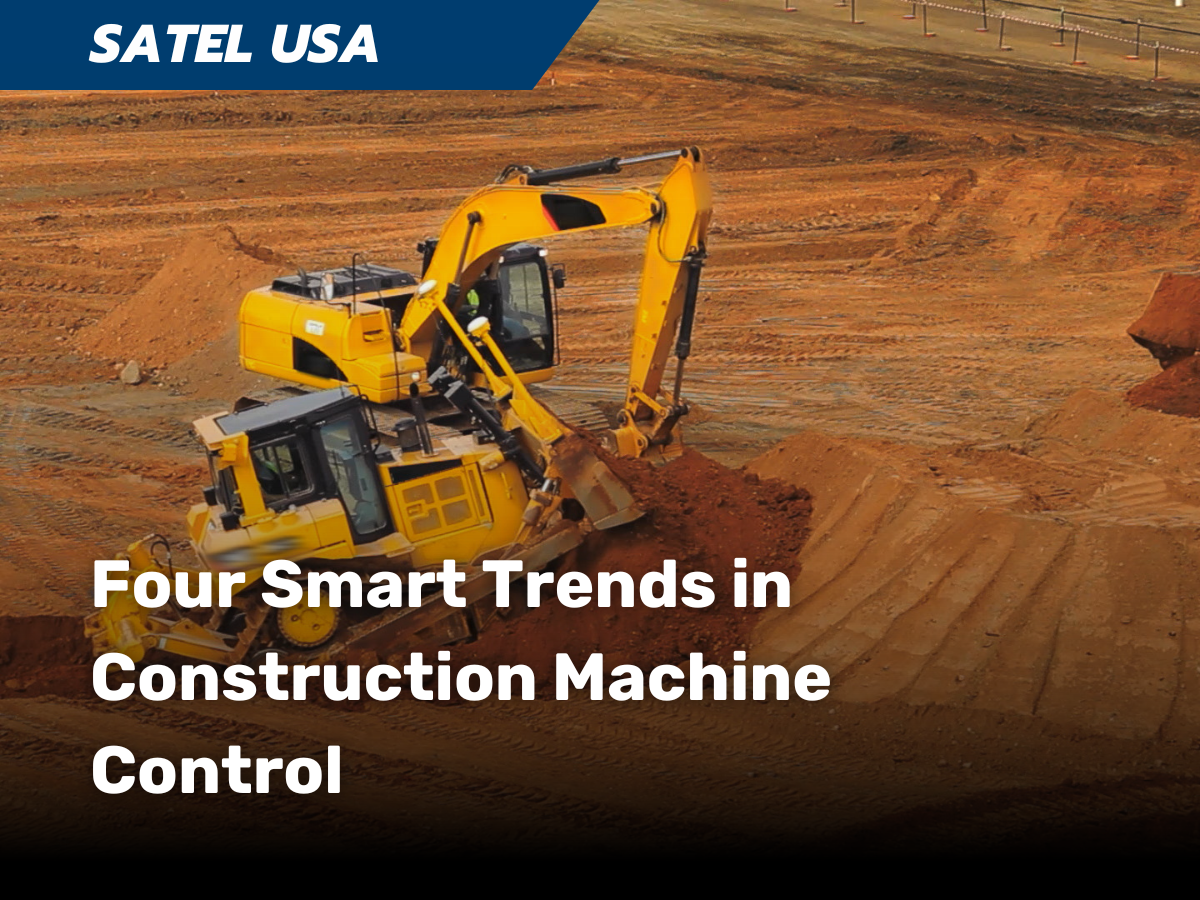
Machine Control Construction sites are becoming smarter and more efficient, thanks to new technology from companies like Caterpillar and Trimble. These advancements are making it easier to work safely and solve the problem of finding skilled machine operators.
Step into the future with Satel USA as we spotlight four transformative trends in construction machine control. Our deep dive reveals not just what these trends are, but how they offer practical solutions, inspire confidence in your projects, and cater directly to your needs. Get ready to be energized by the professional insights and innovative approaches that are shaping a smarter, more efficient construction industry.
Remote Operations: Controlling Machines from a Distance
Caterpillar has developed a system called Cat Command that lets people control big machines like excavators and loaders without having to be inside them. This can be done from as far away as four football fields. This was shown off at CONEXPO-CON/AGG 2023, proving that it’s not just an idea—it’s really happening.
Safety is a big deal with this new tech. As mentioned in For Construction Pros, these technologies are supported and enabled by safety features like radar and camera systems in Cat Detect, ensuring that remote operation does not increase risk. Cat Command is sold in a package that includes:
- Line-of-sight remote control and can also be used in non-line-of-sight remote settings
- Dealer-installed field kits to make a machine Command-ready
- Multiple cameras for non-line-of-site operation and stream on-site video feeds
- A microphone, cameras, indicator lights, a wireless receiver and antenna for mounting on top of the cab
- Advanced features including Grade Assist, Swing Assist and E-Fence
The market for operating construction equipment remotely is so promising that new companies are entering the space to claim their share. Teleo, a startup from Palo Alto established in 2019, is a prime example. It secured $12 million in Series B funding in June 2022, building on an earlier seed round in March 2020. The firm, which employs 20 people primarily in engineering roles, is led by co-founder and CEO Vinay Shet. During the CONEXPO event, Teleo revealed its collaboration with notable new clients such as the John Aarts Group, Teichert, and Tomahawk Construction. Significantly, the company also expanded its network by partnering with dealers across the U.S., Canada, and Europe, setting the stage for its growth in the near future.
Teleo’s remote operation systems are designed with safety as a core feature, ensuring operators have clear visibility at the rear. Shet highlights the use of cameras beneath the bucket to provide clear views of the work zone for those operating wheel loaders and skid steers.
While certain remote control technologies are intended for operators to use within their line of sight, systems like Cat Command and Teleo’s offerings need a reliable internet connection. This connection must be fast enough to allow operators to control equipment in real-time without delays.
Making Machine Operation Easier
Another big step forward is making machines easier to use. SRI International is working on tech that lets operators use simple hand signals or a joystick to control machines. This could make it much simpler for someone who’s never operated a machine before to jump in and start working.
SRI International’s Senior Robotics Engineer, Reuben Brewer, envisions a system where operating an excavator doesn’t require being physically present in it. Operators have the flexibility to control the machinery from the construction site or remotely from another location, such as an office. This is particularly useful when the excavator isn’t being used, allowing the operator to engage in productive work from afar.
Although this concept might seem similar to what Cat Command and Teleo offer, SRI’s research goes beyond just remote control. Brewer emphasizes that their system is unique because it includes the ability to detect humans in the vicinity, allowing the excavator to stop or slow down to prevent accidents. They also immerse the operator in a virtual reality setting for a more effective remote operation experience.
Brewer points out the importance of virtual reality in providing a full sensory experience, which is critical for precision. Initially, without virtual reality, operators missed their target half the time because they lacked depth perception. With virtual reality headsets, they achieved a perfect success rate.
The system’s comprehensive sensory feedback, including 360-degree camera views, is vital for safety, especially in urban settings where the machine automatically shuts down if someone approaches. This safety feature is adaptable, allowing for the creation of no-go zones to prevent the excavator from moving if there’s an obstacle behind it.
Operators can control the excavator using a joystick or simple hand gestures, which mimic the actions they want the machine to perform. This intuitive control method quickly brings new operators up to speed and helps alleviate the labor shortage. Brewer explains that they’ve developed a more natural control pattern that mimics the actual movements, making it easier for operators to perform tasks like scooping and digging, which is especially helpful for those who haven’t operated machinery in a while.
OEM or Aftermarket Machine Control
Fleet owners have a decision to make when it comes to the type of machine control technology they use, whether it’s for remote operation, precision grading with GNSS, or tech that allows machines to interact with their environment. They can either go with systems provided by the original equipment manufacturer (OEM) or choose from solutions offered by third-party vendors after purchase.
According to the 2023 State of the Industry Construction Technology Report, the trend is leaning towards automation technologies that are either built into the equipment by the OEM or added later by third-party companies like Trimble, Leica, Unicontrol, and Teleo. The majority of the industry professionals surveyed are leaning towards OEM-provided controls, with 27% already using them, 5% allocating funds for them, and 11% planning to adopt them in the future. In contrast, 15% are using third-party machine controls, with an equal 5% budgeting for them and a slightly lower 12% considering them for future use.
Contractors might prefer OEM solutions to minimize the risk of damaging sensitive equipment during installation. The ease of purchasing and the potential for a higher resale value of machines equipped with OEM technology are also persuasive factors. Caterpillar, for instance, is progressively including machine control features like grade control as standard on certain models, such as hydraulic excavators. Case is also providing a universal machine control option compatible with major tech providers, including Topcon, Trimble, and Leica Geosystems.
Even though built-in machine control options are currently more widely used, the growing presence of third-party providers like Unicontrol, Sodex, Teleo, and others suggests that the market for retrofitting machine control may expand. As more OEMs begin to standardize machine control features, the industry may continue to favor OEM solutions, or the trend could stabilize. The industry is keeping an eye on this development to see whether the convenience of OEM-integrated machine control outweighs the benefits of third-party options.
Machine Control Data: The Secret to Smarter Construction
None of this would work without data. Another trend shaping the construction machine control landscape is the growth of technology that prepares data for machine control systems and gathers information for progress tracking and final construction reports.
Trimble Earthworks stands out as a leading solution for these tasks, offering the capability for users to send files straight to machines on-site either wirelessly through Trimble WorksManager software or via a USB drive with the File Flipper app.
There are also other tools available for managing machine control data. InSite Software’s InSite Elevation Pro, for example, underwent a major overhaul in 2020 to enhance its user-friendliness and performance. The platform continues to evolve, with the recent introduction of RockAlert in April 2023. This feature provides machine control systems with valuable data on the presence of rocks, water, and other underground layers.
Additionally, Quantum Land Design introduced the Quantum Flight Pack in April 2023. This tool allows contractors to set ground control points with a GPS rover, automate drone flights to survey the area, and then process the collected drone data to perform volume measurements for project planning.
Conclusion:
As we navigate the evolving terrain of construction technology, it’s evident that the industry is not just building structures—it’s building a smarter future. The four smart trends in machine control we’ve discussed are not just reshaping the landscape; they’re providing tangible solutions to real-world challenges such as the skilled labor shortage and on-site safety concerns.
At the heart of this technological revolution, companies like Caterpillar are driving innovation, ensuring that construction sites are not only more efficient but also more interconnected. And while Satel USA may not produce complete machine control systems, our expertise in robust communication technology positions us as a cornerstone in this dynamic ecosystem.
Our Satel radios are the silent heroes behind the scenes, providing the reliable communication that is critical for advanced machine control systems to function seamlessly across vast distances and challenging environments.
Discover how our Satel radios can amplify the effectiveness and reliability of your machine control operations. Visit our Machine Control Page today!